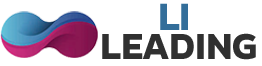
Manufacturing of Prototypes for ITER First Wall Panels (FWP):
ITER is the biggest international experiment to explore the potential of fusion energy at such scale bringing together seven parties. Europe is responsible for nearly half of the project and is the host. China, Japan, India, the Republic of Korea, the Russian Federation, and the United States are also contributing.
LEADING has been involved since 2012 in the manufacturing of different mock-ups, a semi-prototype, and a full-scale prototype for the ITER FWP.
The FWP are the detachable, front-facing elements of the blanket that are designed to withstand the heat flux from the plasma. These highly technological components are made of beryllium tiles bonded with a copper alloy and 316L (N) stainless steel.
Prototype Development Stage:
LEADING, in collaboration with IBERDROLA and JACOBS, developed the preliminary FWP prototypes through two contracts awarded by Fusion for Energy (F4E), the European Union’s (EU) organisation responsible for Europe’s contribution to ITER:
Series Manufacturing Stage:
LEADING and EMPRESARIOS AGRUPADOS established in 2020 the company Fusion Business Leadership in order to implement the production of a first batch of FWP industrial series, through the following contract, also awarded by Fusion for Energy (F4E):
DYNAMIC to perform the ITER Tokamak Assembly (TAC2):
The ITER Organization has awarded a contract, for a global value above 200 M€, for the Tokamak Assembly (TAC2) to DYNAMIC, a company created specifically for the purpose of guaranteeing the seamless execution of the work by the collective contributions of its founding members: Ansaldo Nucleare, Endel Engie, Orys Group ORTEC, SIMIC, Leading and Ansaldo Energia.
The operation will mostly be performed at the ITER site in Cadarache, with the engineering and manufacturing support of DYNAMIC’s founding companies. It will include complex lifting, positioning, welding and inspection of some of the largest and most precious components and subsystems such as the toroidal field coils, vacuum vessel sectors, thermal shields and ports, first in the Assembly Hall and then in the central Tokamak Pit.
“For most of the Companies who joined forces within DYNAMIC, this installation phase is the continuity of years of activities for the ITER project already serving either as designer, manufacturer or installation service provider. It is this experience we have to integrate with the CMA/IO team to make this first-of-a-kind challenge a technical success, with the highest standards of quality and safety,” said Francesco Maestri CEO of Ansaldo Nucleare.
“We are pleased to take this next step forward toward Assembly Phase,” said Bernard Bigot, Director-General of ITER. “We are entering a critical time, with the need to assemble and install equipment procured by all ITER Members, with exceptionally demanding specifications which have to be met with high precision, within a quite challenging schedule. We trust that DYNAMIC will complete their tasks according to our best expectations. It is critical for the success of ITER”.
Supply of the splice plates for the assembly of the JT-60SA TF Magnet Outer Intercoil Structure (F4E-OPE-805):
Rapid ‘just-in-time’ custom machining of each of the 18 sets of 10 splice plates according to measurements supplied by F4E from the installed positions of the TF coils and fast delivery of each set of customised splice plates individually to the QST Fusion Research Site in Naka, Japan.
Manufacturing of Prototypes for the Supports of the BCM System F4E-OPE-899:
Manufacture and supply of prototypes of pipe supports for the Blanket Cooling Manifold (BCM) system. The blanket modules are the part of the ITER machine that acts as a first barrier and protects the vacuum vessel, which is the heart of the ITER machine, from the neutrons and heat produced by the hot plasma during the fusion reaction. The cooling of the blanket modules is ensured by the Blanket Cooling Manifolds which are connected to the Tokamak Cooling Water System (TCWS) and provides pressurised cooling water to the Blanket system. The BCM system is based on the multi-pipe concept, consisting of bundles of separate stainless-steel pipes running inside recesses at the back of the blanket modules. The scope of the supply also includes the coating with alumina of pieces of pipes to be assembled with the support.
Detail Design of the Manufacturing Process for the Jules Horowitz Reactor (JHR):
The main activities developed were the following: Definition of the manufacturing process from the raw material till assembly, control and machining operations; Identification of suppliers for semi-finished and finished products; Definition of the main manufacturing phases according to RCC Code; FEM calculations to guarantee deformation and stresses under yield strength during manufacturing operations; GD&T activities for all drawings to assure the assembly of all components; Definition of means associated to manufacturing (tooling, machining fixtures, etc.); Definition of means for assembly and adjustment.